CONTROL UNITS
Welding process controllers,
experts in communication.
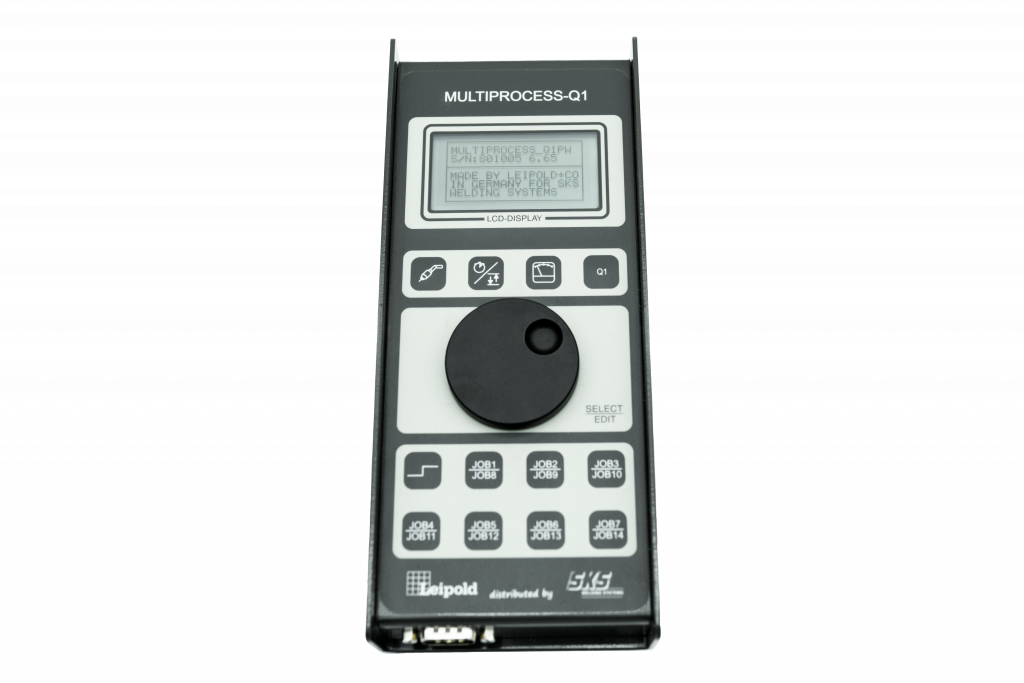
Q1
Manual welding controller
The Q1 is a welding process controller, designed for manual welding tasks with Leipold power sources (LSQ). Our welding process controllers calculate optimal welding parameters based on material, filler metal, wire feed speed and gas type. The Q1 can handle multiple welding processes such as MIG, MAG, I-pulse, U-pulse, KF-pulse, TIG and TIG-pulse. It has automatic compensation of welding parameters (AutoComp) to adapt to environmental changes like temperature, air draft, torch position offset and so on. Device Setup and data backup are simplified by our Q1-Tool software.
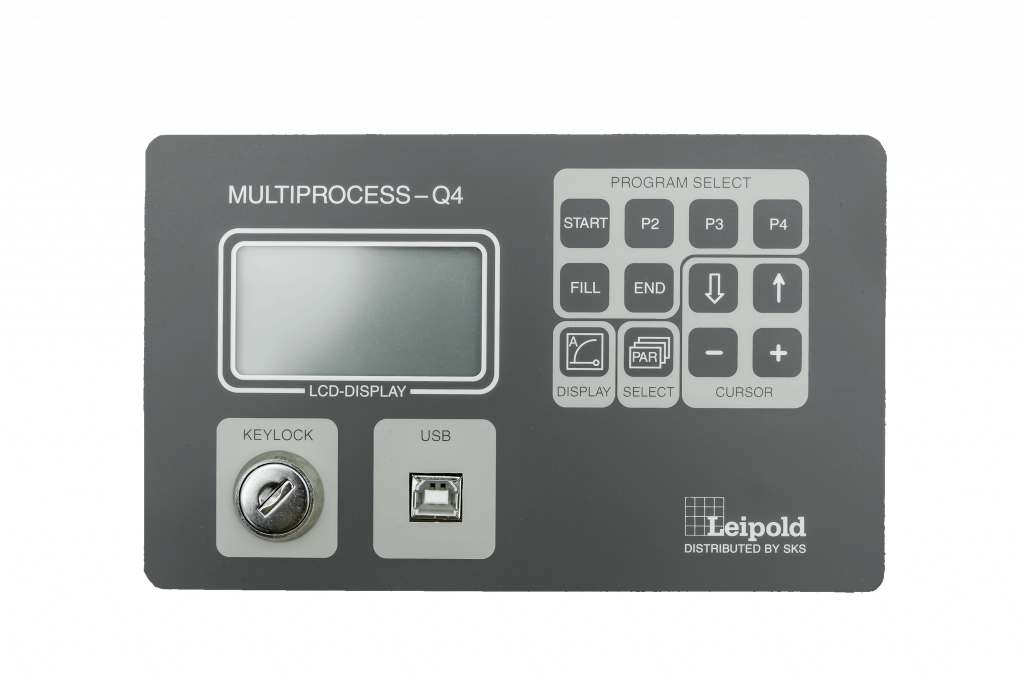
Q4
Controller in the power source
The Q4 is an entry-level welding process controller, integrated into a Leipold power source (LSQ) which causes a simplified overall system setup that results in a low price. Our welding process controllers calculate optimal welding parameters based on material, filler metal, wire feed speed and gas type. The Q4 can handle multiple welding processes such as MIG, MAG, I-pulse, U-pulse, KF-pulse, microMIG, TIG and TIG-pulse. It has automatic compensation of welding parameters (AutoComp) to adapt to environmental changes like temperature, air draft, torch position offset and so on. In combination with a robot the Q4 is able to automatically synchronize welding parameters with the TCP velocity (SynchroWeld). Setup and data backup can be eased by using our Q8-Tool software.
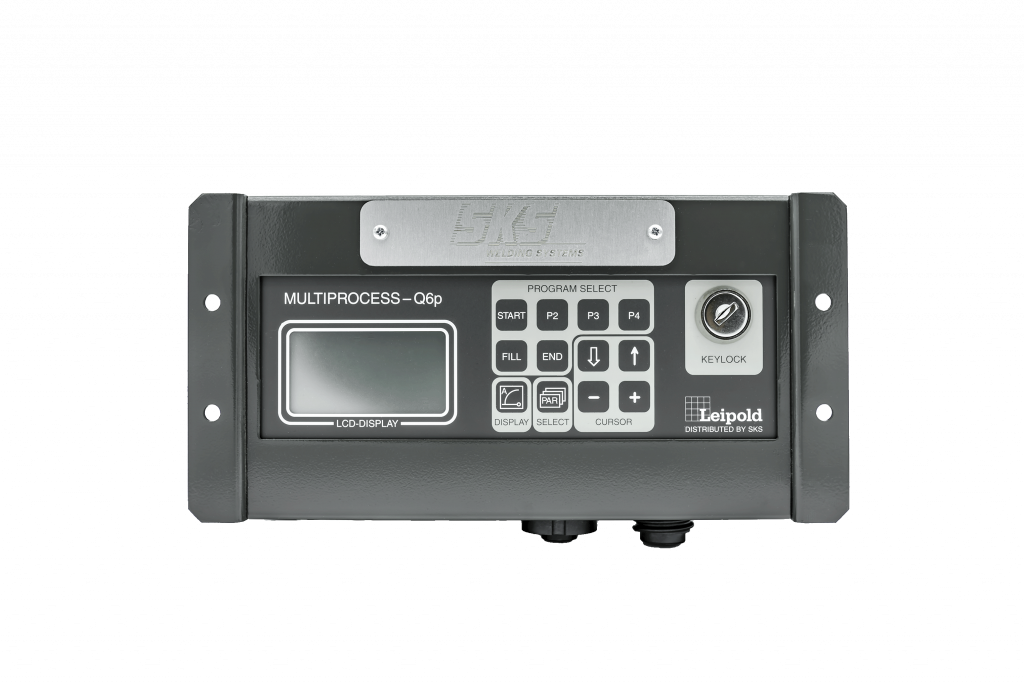
Q6pw
Entry-level local controller
The Q6pw welding process controller is a cost-effective entry-level device. Our welding process controllers calculate optimal welding parameters based on material, filler metal, wire feed speed and gas type. The Q6pw can handle multiple welding processes such as MIG, MAG, I-pulse, U-pulse, KF-pulse, microMIG, TIG and TIG-pulse. It has automatic compensation of welding parameters (AutoComp) to adapt to environmental changes like temperature, air draft, torch position offset and so on. In combination with a robot the Q6pw is able to automatically synchronize welding parameters with the TCP velocity (SynchroWeld). Setup and data backup can be eased by using our Q8-Tool software.
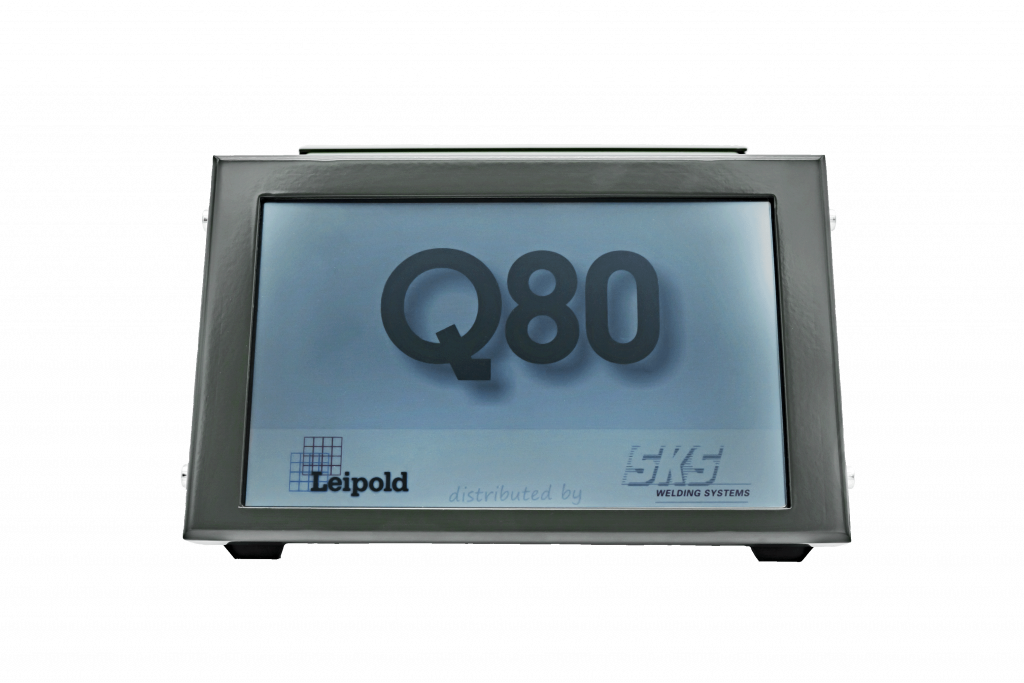
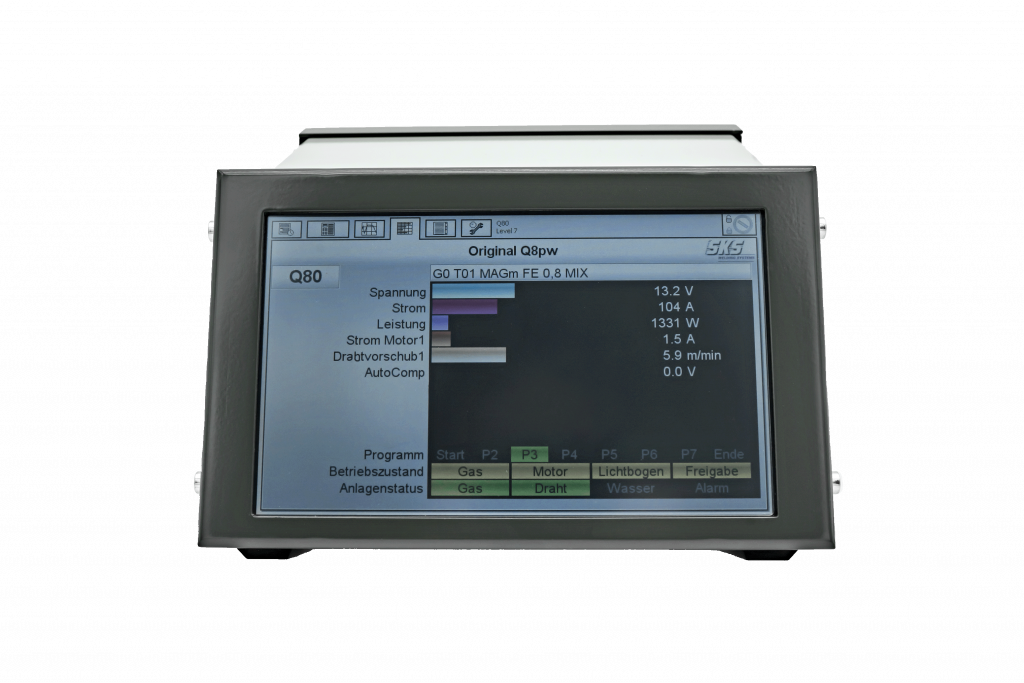
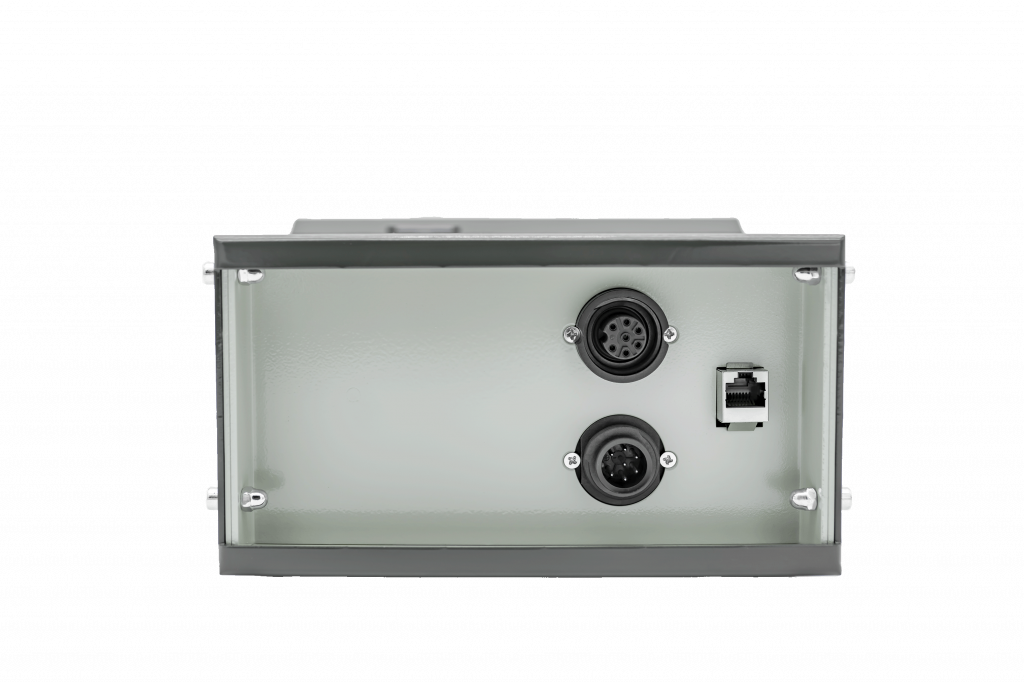
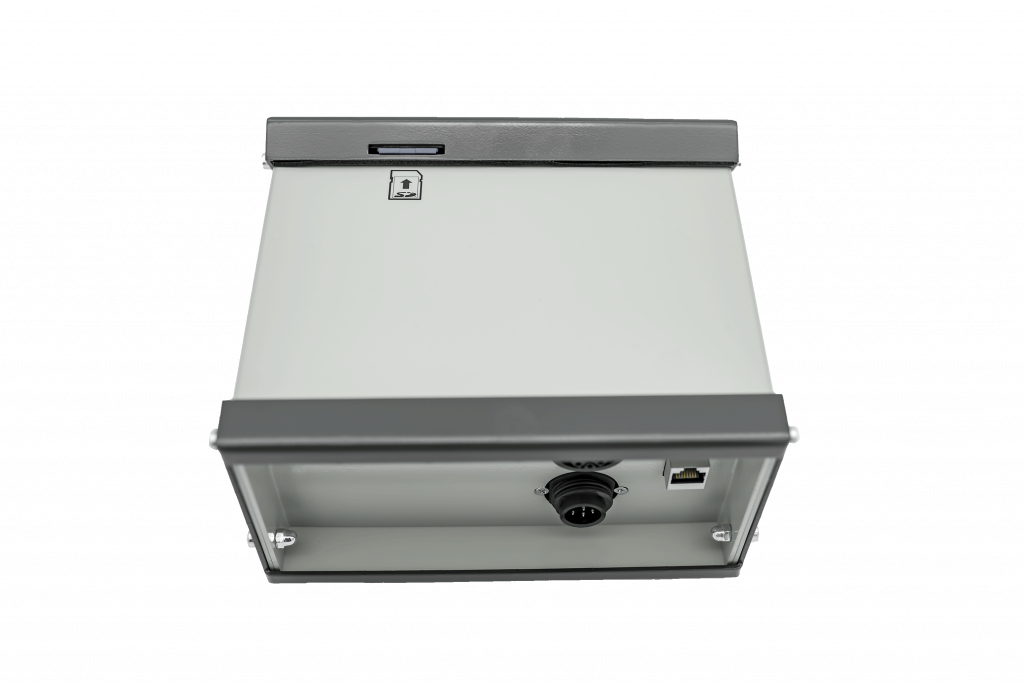
Q80
Universal controller
with touch
The Q80 welding process controller is a central management device for one welding system that provides the interface between operator, PC and welding equipment. With touch screen based operation and a graphical user interface the Q80 is simple and easy to use. Our welding process controllers calculate optimal welding parameters based on material, filler metal, wire feed speed and gas type. The Q80 can handle multiple welding processes such as MIG, MAG, I-pulse, U-pulse, KF-pulse, microMIG, TIG and TIG-pulse. It has automatic compensation of welding parameters (AutoComp) to adapt to environmental changes like temperature, air draft, torch position offset and so on. In combination with a robot the Q80 is able to automatically synchronize welding parameters with the TCP velocity (SynchroWeld). The Q80 let’s our welding system talk to the outside world using Ethernet. With our software Q8Tool you can do central or de-central data management, backups, record and store data of all welded seams. Q8Tool optionally provides a DCOM Interface to connect standard Software, even Word or Excel, to our welding systems. The Q80 speaks fluently MQTT and OPC-UA. With an optional license the Q80 will store all welding data completely internally, ready to be used by our visualization software Q8xRemote.
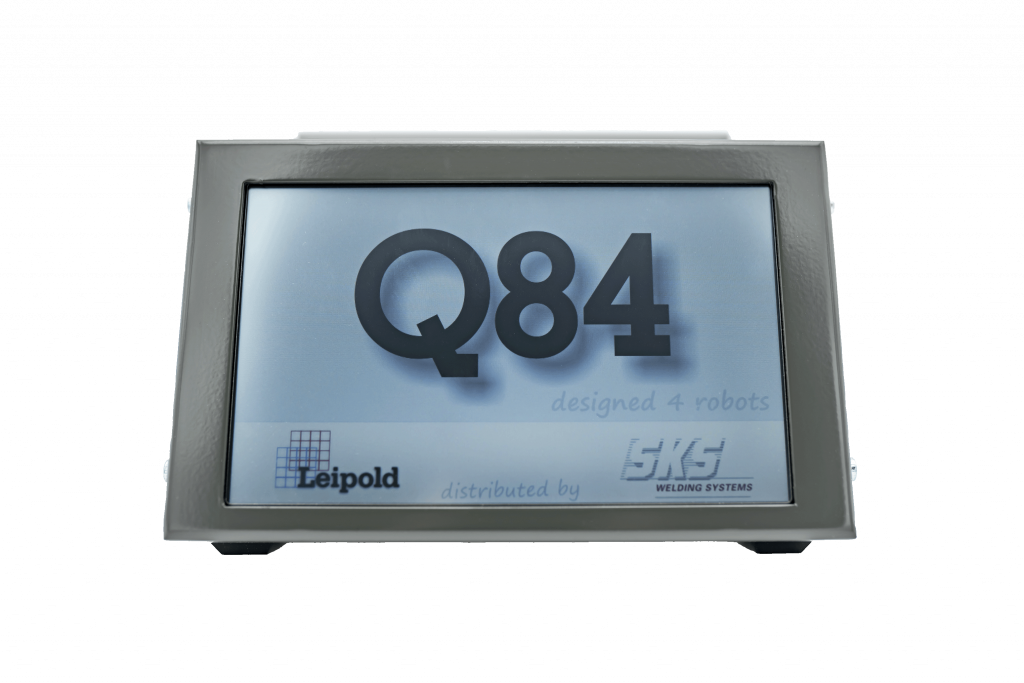
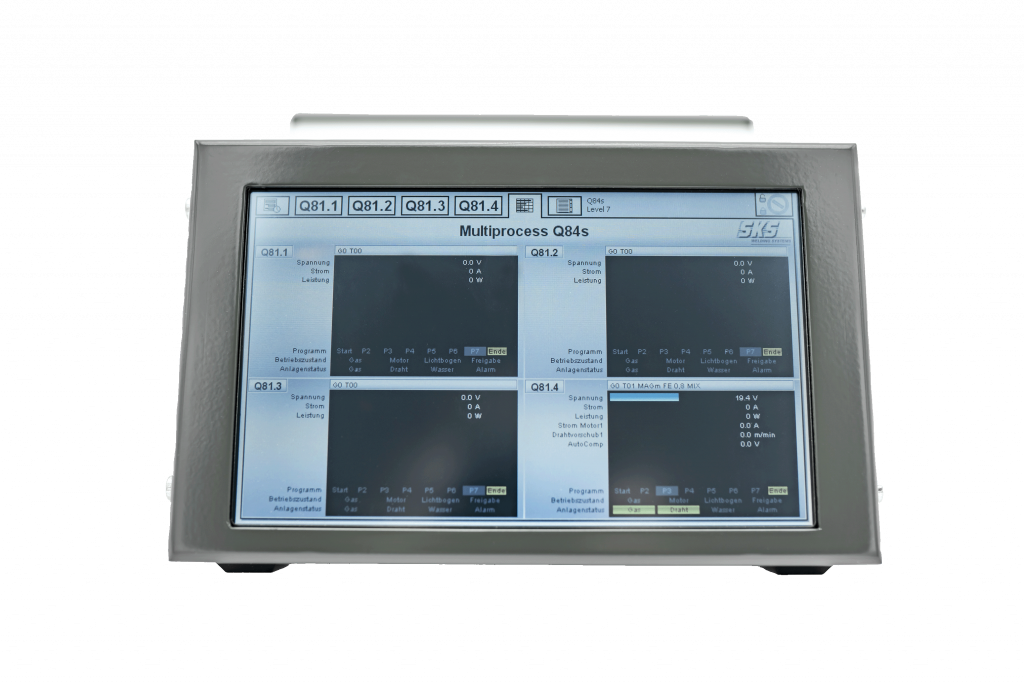
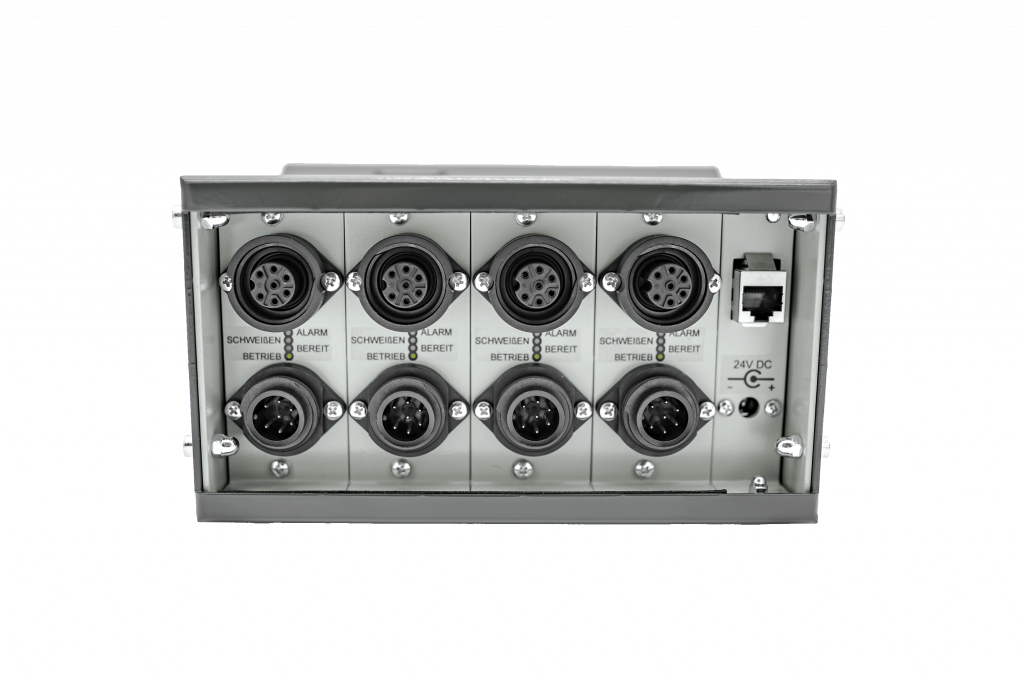
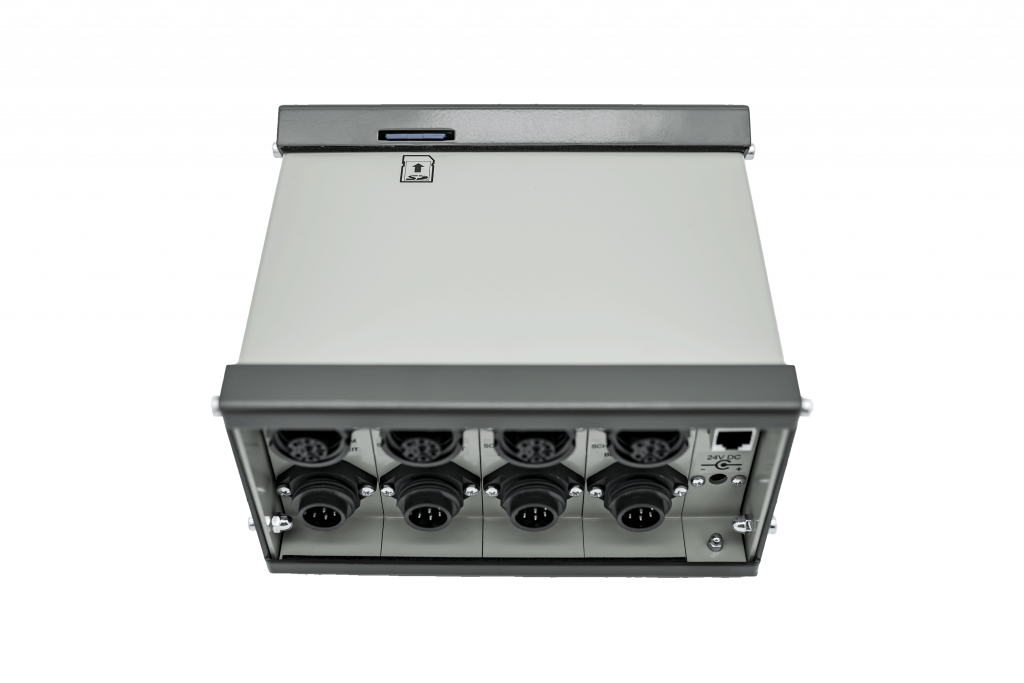
Q84s
Q80 for four
The Q84s welding process controller is a central management device for four welding systems that provides the interface between operator, PC and welding equipment. It has identical functionality as the Q80, but is more affordable than multiple Q80’s when running more than one welding system. With touch screen based operation and a graphical user interface the Q84s is simple and easy to use. Our welding process controllers calculate optimal welding parameters based on material, filler metal, wire feed speed and gas type. The Q84s can handle multiple welding processes such as MIG, MAG, I-pulse, U-pulse, KF-pulse, microMIG, TIG and TIG-pulse. It has automatic compensation of welding parameters (AutoComp) to adapt to environmental changes like temperature, air draft, torch position offset and so on. In combination with a robot the Q84s is able to automatically synchronize welding parameters with the TCP velocity (SynchroWeld). The Q84s let’s our welding system talk to the outside world using Ethernet. With our software Q8Tool you can do central or de-central data management, backups, record and store data of all welded seams. Q8Tool optionally provides a DCOM Interface to connect standard Software, even Word or Excel, to our welding systems. The Q84s speaks fluently MQTT and OPC-UA. With an optional license the Q84s will store all welding data completely internally, ready to be used by our visualization software Q8xRemote.
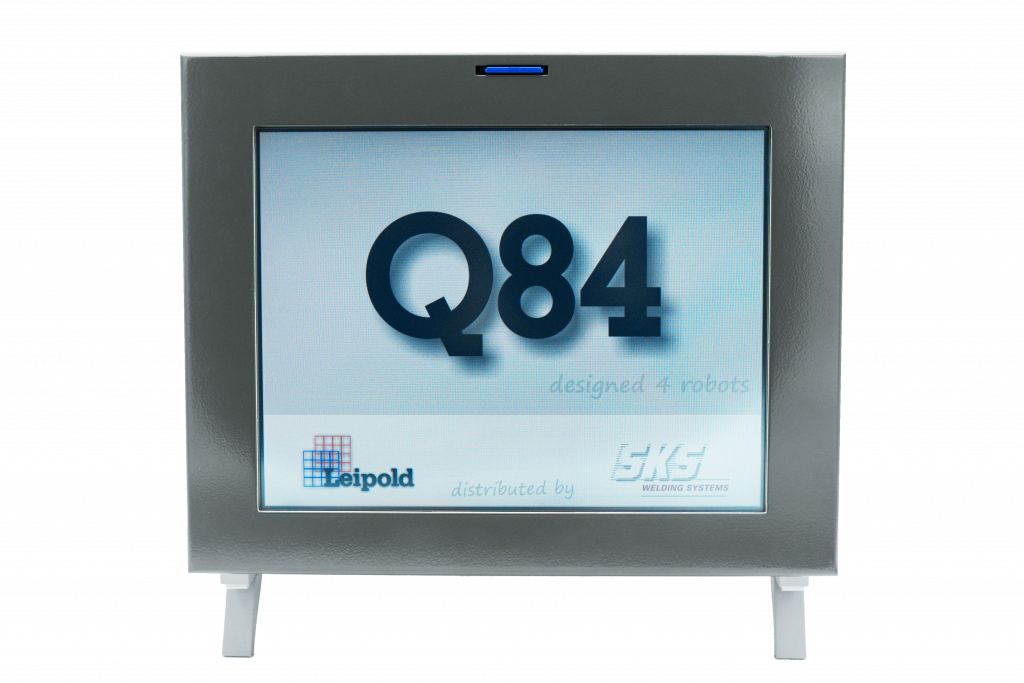
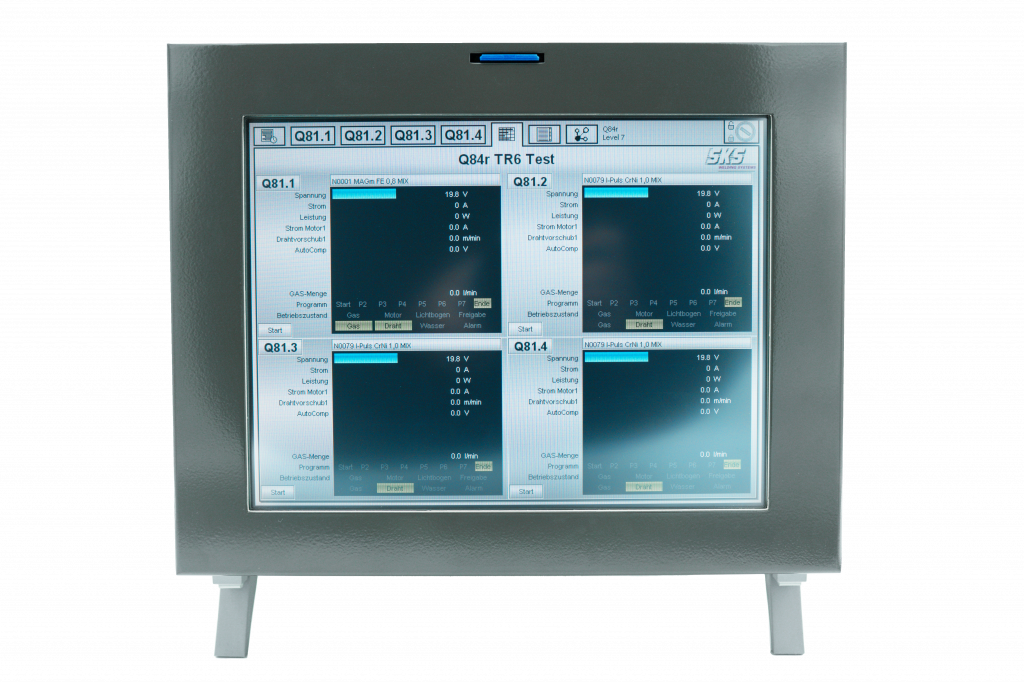
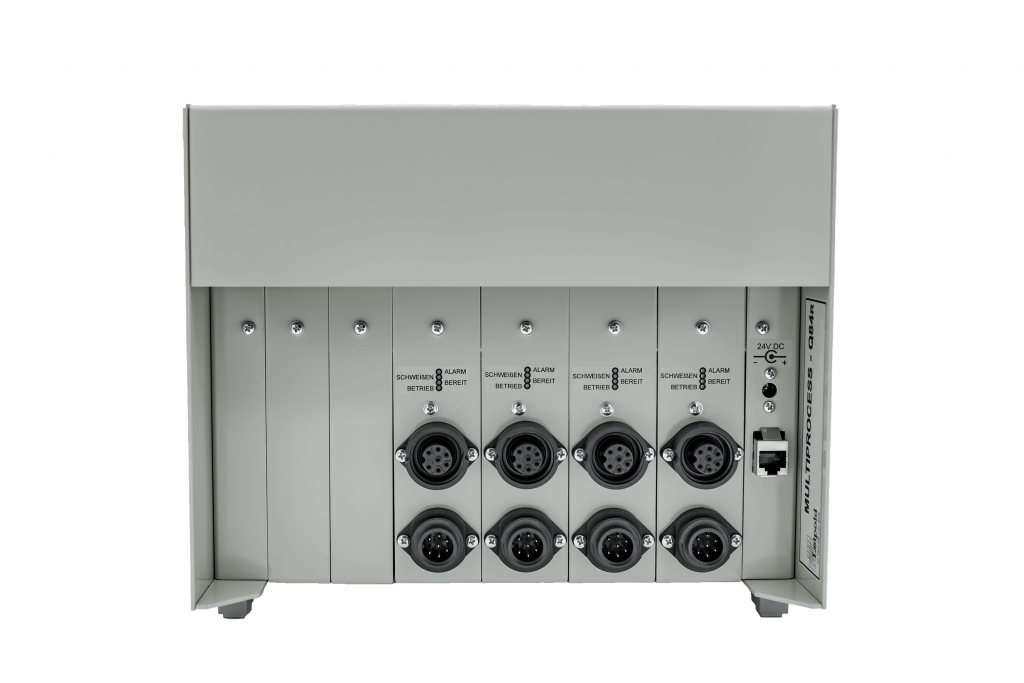
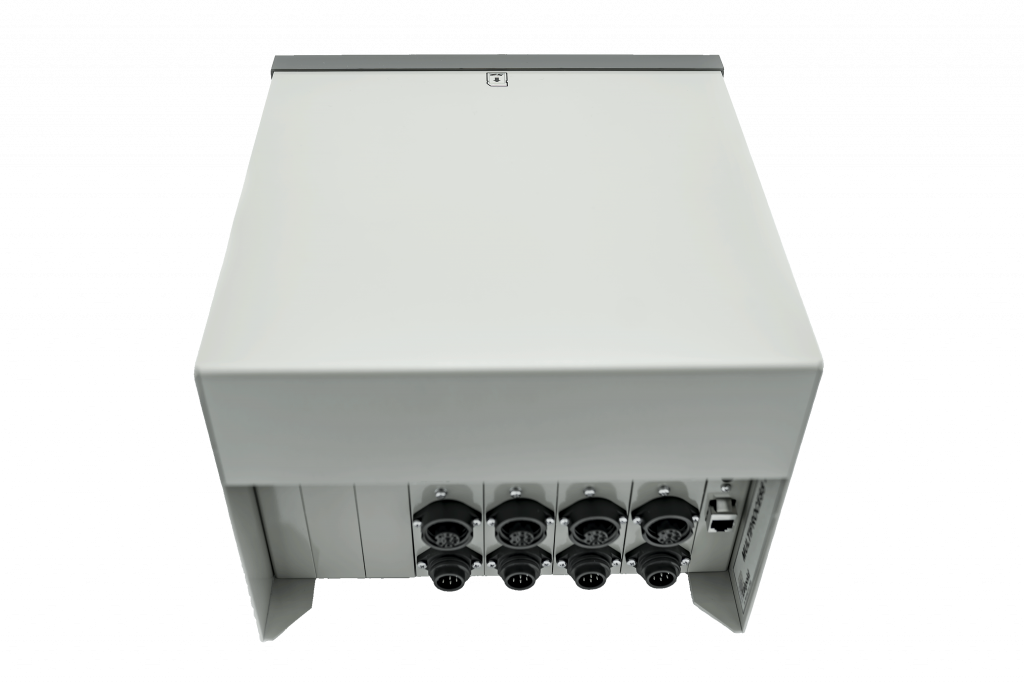
Q84r
Q84s but bigger and faster
The Q84r welding process controller is a central management device for four welding systems that provides the interface between operator, PC and welding equipment. It is functionally identical to the Q84s, but it has a bigger screen and can be equipped with faster CPUs. With touch screen based operation and a graphical user interface the Q84r is simple and easy to use. Our welding process controllers calculate optimal welding parameters based on material, filler metal, wire feed speed and gas type. The Q84r can handle multiple welding processes such as MIG, MAG, I-pulse, U-pulse, KF-pulse, microMIG, TIG and TIG-pulse. It has automatic compensation of welding parameters (AutoComp) to adapt to environmental changes like temperature, air draft, torch position offset and so on. In combination with a robot the Q84r is able to automatically synchronize welding parameters with the TCP velocity (SynchroWeld). The Q84r let’s our welding system talk to the outside world using Ethernet. With our software Q8Tool you can do central or de-central data management, backups, record and store data of all welded seams. Q8Tool optionally provides a DCOM Interface to connect standard Software, even Word or Excel, to our welding systems. The Q84r speaks fluently MQTT and OPC-UA. With an optional license the Q84s will store all welding data completely internally, ready to be used by our visualization software Q8xRemote.